Revolutionizing Logistics: The Power of Predictive Maintenance in Automation
Discover how predictive maintenance enhances logistics automation by reducing downtime, improving efficiency, and boosting customer satisfaction through advanced technology integration.
The Role of Predictive Maintenance in Enhancing Logistics Automation
Predictive maintenance is a strategy that anticipates equipment failures before they occur, significantly reducing downtime and enhancing operational reliability in logistics. By leveraging advanced technologies, predictive maintenance allows logistics companies to shift from a reactive maintenance model to a proactive one, which is essential in today’s fast-paced supply chain environment. With the growing complexity and demands of logistics operations, this approach not only minimizes disruptions but also enhances the overall efficiency of logistics processes.
Technologies such as the Internet of Things (IoT), artificial intelligence (AI), and machine learning play a pivotal role in the successful implementation of predictive maintenance strategies. For instance, IoT sensors installed in warehouse equipment can continuously monitor the health of machinery, providing real-time data that informs maintenance needs. This capability helps logistics managers make timely decisions, optimizing resource allocation and ensuring that equipment is maintained based on actual usage and condition rather than fixed schedules.
Definition and Importance of Predictive Maintenance
Predictive maintenance is defined as a proactive approach that utilizes real-time data analytics to forecast equipment malfunctions, transitioning from traditional reactive maintenance practices. This approach is becoming increasingly important, especially considering that over 50% of industrial facilities still operate under a run-to-failure model, which can lead to costly downtime and inefficiencies. By focusing on maintaining equipment based on data-driven insights, logistics companies can optimize maintenance costs and resource allocation, ultimately improving asset management within their operations.
The significance of predictive maintenance extends beyond mere equipment upkeep; it fundamentally enhances operational reliability and service levels. For example, companies that implement predictive maintenance can experience a marked improvement in delivery performance, as timely interventions prevent breakdowns that could disrupt logistics processes. This shift not only reduces costs associated with unplanned downtime but also leads to enhanced customer satisfaction through more reliable service delivery.
Technologies Enabling Predictive Maintenance
Several key technologies enable the effective implementation of predictive maintenance in logistics. IoT sensors are at the forefront, allowing for the continuous monitoring of equipment health, which aids in timely repairs and minimizes unnecessary inspections. These sensors collect data on various parameters such as temperature, vibration, and performance metrics, which can signal impending failures. For instance, if a conveyor belt in a warehouse exhibits unusual vibrations, the IoT system can alert maintenance personnel to address the issue before a complete failure occurs.
Artificial intelligence enhances predictive maintenance by analyzing data collected from these sensors to identify potential failures and inform maintenance scheduling. Predictive analytics further supports logistics operations by enabling accurate forecasting and proactive management of transportation resources. Machine learning algorithms continuously refine their predictions based on historical data patterns, leading to progressively better maintenance outcomes. Additionally, the integration of Natural Language Processing (NLP) can extract insights from maintenance logs and customer feedback, bolstering predictive capabilities.
Benefits of Predictive Maintenance in Logistics
The benefits of implementing predictive maintenance in logistics are substantial. For instance, companies that adopt these strategies can increase vehicle uptime by up to 25% and save approximately $2,000 per vehicle annually. Moreover, predictive maintenance helps prevent breakdowns, which can save logistics firms hundreds of thousands of dollars in penalties for missed deliveries, ultimately protecting their bottom line.
Beyond immediate cost savings, predictive maintenance also extends the lifespan of equipment and enhances operational efficiency over time. By minimizing operational disruptions and optimizing maintenance schedules, logistics companies can ensure smoother processes and improve safety by reducing the risks associated with equipment failures during operations. Furthermore, the ability to proactively address maintenance needs fosters a culture of continuous improvement within logistics operations.
Case Studies of Successful Implementation
Several companies have successfully integrated predictive maintenance into their logistics processes, demonstrating its effectiveness in enhancing operational efficiency. DHL, for example, has invested $350 million in digitization and predictive analytics to improve global supply chain visibility and streamline logistics operations. Similarly, Maersk has utilized predictive analytics for better container repositioning, leading to significant savings in operational costs.
Ford Motor Company has reported substantial improvements in vehicle reliability due to AI-driven predictive maintenance systems, while Amazon employs these strategies to enhance fleet management, effectively reducing delivery times and operational costs. Transmetrics also assists logistics companies in leveraging predictive analytics to optimize operations, resulting in improved efficiency for their clients. These case studies underscore the transformative potential of predictive maintenance in logistics.
Future Trends in Predictive Maintenance
The future of predictive maintenance in logistics is poised for significant growth, driven by advancements in automation and data analytics. As logistics operations increasingly rely on real-time monitoring capabilities, the demand for predictive maintenance strategies is expected to rise. Continuous learning from data will further enhance prediction accuracy and maintenance efficiency, adapting to evolving operational needs over time.
Investments in predictive analytics tools are projected to increase, with a large majority of third-party logistics providers expected to adopt such technologies. Future advancements in AI and machine learning will refine predictive maintenance algorithms, allowing for even more precise forecasting and resource management. Furthermore, as sustainability becomes a priority, predictive maintenance can contribute to greener logistics practices by optimizing resource use and reducing waste.
The Impact of Predictive Maintenance on Logistics Performance
Integrating predictive maintenance into logistics automation is essential for enhancing efficiency, reducing costs, and improving overall service levels. Companies that focus on high-quality data and consider hiring data experts to implement predictive maintenance solutions effectively can achieve a competitive edge in the market. By meeting service level agreements (SLAs) and enhancing customer satisfaction, businesses adopting predictive maintenance foster a culture of continuous improvement and innovation within their logistics operations, ultimately supporting long-term growth.
The impact of predictive maintenance extends beyond operational metrics; it fundamentally reshapes how logistics companies manage their resources and deliver services, leading to enhanced reliability and performance across the supply chain.
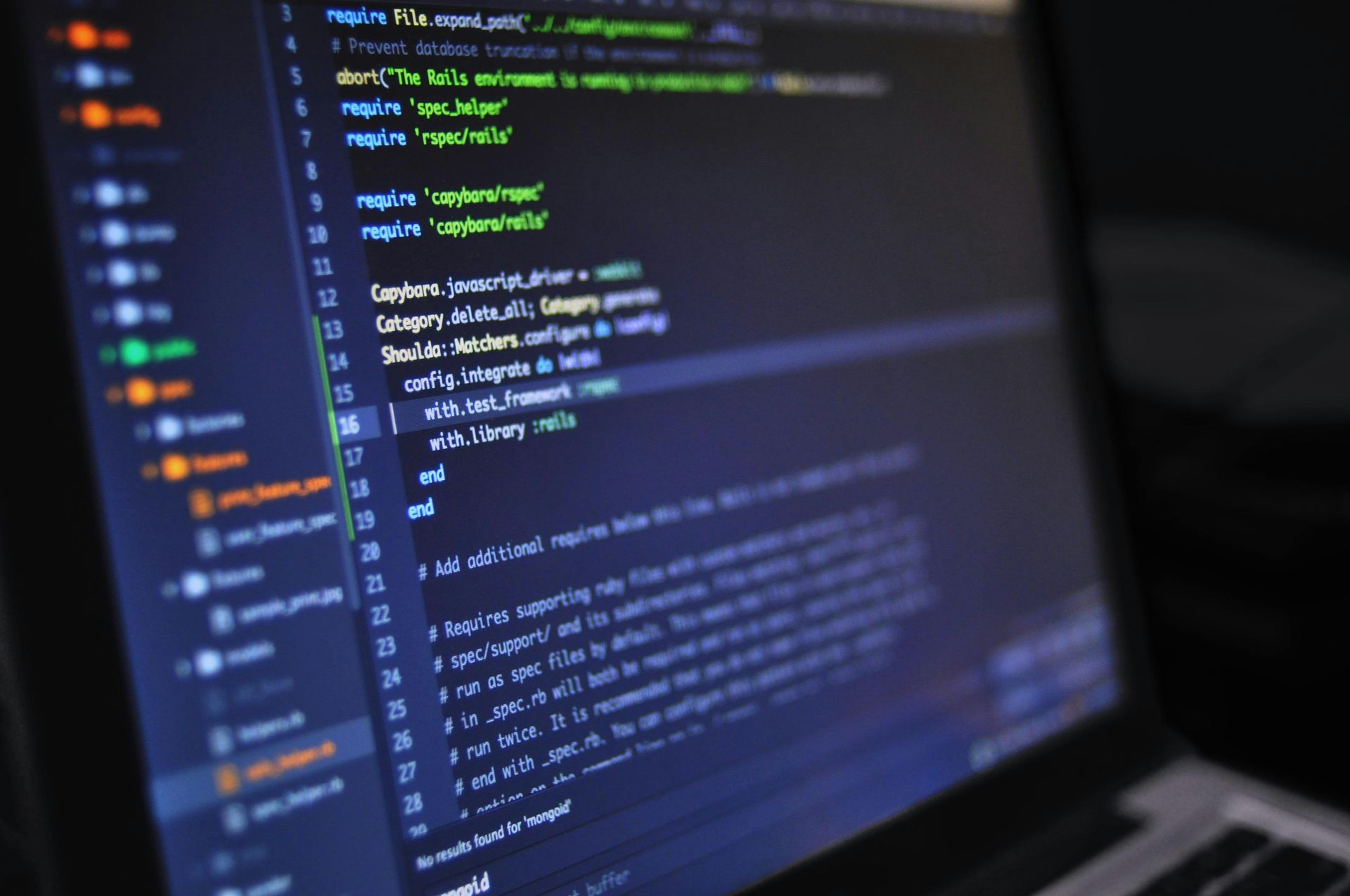
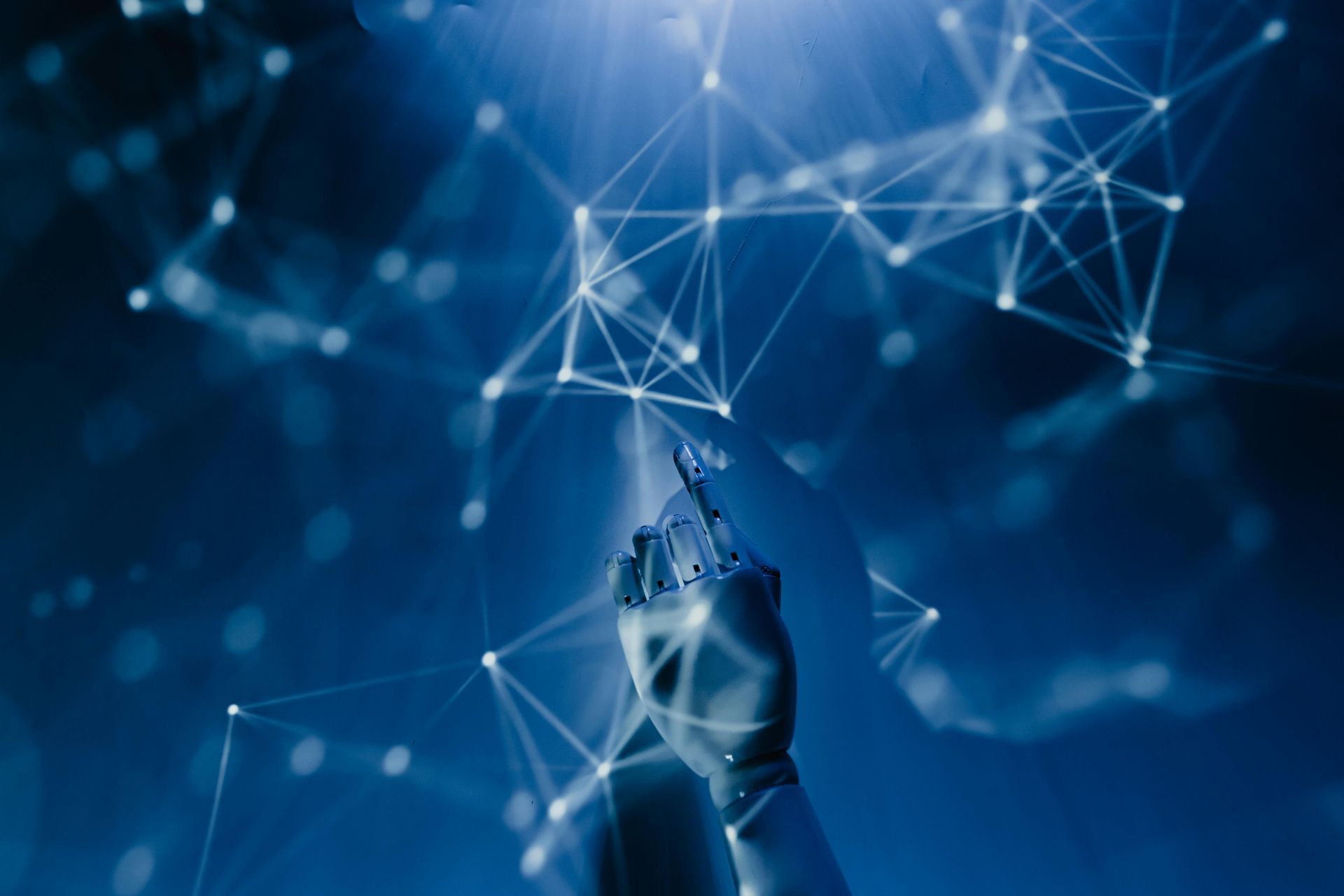